Merry
Christmas
Friends in the Name of Safety:
Serving You! Friends, what
can we say? You have allowed our
staff to come into your workplace
and become part of your families. We consider ourselves blessed and
humbled to work with so many great
people across this state.
Our services have been
embraced by your employees, our
workshops have been well attended,
we have begun several new programs
this past year and you have
supported them completely.
The
best news is that accidents are
being prevented, workers' comp
claims are being reduced and workers
are going home safely! Oh, and your
employers are not having to pay out
additional money to provide these
services to their employees. The NC
Industrial Commission Safety
Education Section is providing these
services to you as yet another
service from the State of North
Carolina.
As you are aware, the state
budget is in dire straits. As our
elected officials begin to seek ways
to reduce expenditures, they are
examining all areas of state
government. We are asking for your
assistance to procure letters from
businesses where we have provided
training stating whether or not the
training is helping or has helped
reduce injuries and accidents in
your facilities. We are
particularly interested in the
percentage of reduction in Workers'
Comp Costs and injuries - we don't
necessarily need actual numbers
aside from the percentage of
reduction in injuries, reduced costs
by _____%, etc...
Please
send to Dennis' email address at
Dennis.Parnell@ic.nc.gov
and your support will be greatly
appreciated!
We are still trying to finalize our
2009 APCAP schedule. We will be
adding an
ADVANCED APCAP in 2009. In
order to participate, you must have
completed the basic 30-hour APCAP. The ADVANCED APCAP will be two days
of intense training to further
assist you with your Safety & Health
program.
In 2009, we will offer
BOTH
COURSES concurrently on the
same date and location in order to
better serve you.
Here
are the
UPDATED "PROPOSED" DATES AND
LOCATIONS for 2009:
-
February 9 - 13, 2009 -
Fayetteville, NC
-
March 9 - 13, 2009 - Wilmington,
NC
-
June 15 - 19, 2009 - Smithfield,
NC
-
August 17 - 21, 2009 - Flat
Rock, NC
-
August 31 - September 4, 2009 -
Atlantic Beach, NC
-
October 26 - 30, 2009 - Asheboro
Zoo, Asheboro, NC
We look forward to
seeing you at one of our programs in
2009. Again, let us say "THANK YOU"
for allowing us to be a part of your
family.
Your
REGIONAL SAFETY COUNCILS are
continuing to work for you, so
please refer to the calendar section
of our Safety Bulletin for more
information. Please support YOUR
councils!
As always, we thank you for your
support and we pledge to continue to
serve your needs. We promise to
continue to provide quality ACCIDENT
PREVENTION training programs.
|
Have a
plan in case of disaster!
Floods,
hurricanes, tornadoes, and fires are
just a few of the phenomena that
have caused people to lose their
homes, their possessions, and
sometimes even their lives. While
you often can't prevent them, you
can be prepared for them.
While most people know that they
should have an escape route mapped
out in case of a fire, or a
designated place to go in case of a
tornado, these and other disasters
might require you to think in a bit
more detail. To be as prepared as
possible, considered the following
questions:
- Have you had first aid or CPR
training in the past year?
- Do you have a designated meeting
place or an emergency contact person
(preferably outside of your
geographic area) in case your family
becomes separated?
- Where will your pets go?
- Do you have a disaster supply kit
with enough food and water for 3
days?
- Is your first aid kit complete?
|
Air Contaminants:
Know your limits!
When you work with hazardous
chemicals, the air around you can
become contaminated. OSHA sets
exposure limits to ensure that
employees breathe safe air while
they work.
OSHA's air contaminants standard
lists various chemicals along with
their permissible exposure limits (PELs).
PELs are the highest amount of an
air contaminant that employees can
safely be exposed to for a certain
amount of time. Your employer must
tell you the hazards of the
chemicals you work with, including
the hazards associated with air
contaminants.
To keep exposures at or below the
PELs, employers use engineering or
administrative controls. An example
of an engineering control is exhaust
ventilation equipment. An example of
an administrative control is
substituting a less toxic chemical.
If these methods don't provide
enough protection, employees must
wear respirators or other types of
personal protective equipment.
You can find exposure limit
information on a chemical's material
safety data sheet.
|
NCIC Video
Library
Check out our
Video Library !
Finally! We
have completed UPDATING our online
Video/DVD listings. The new listings
are in
RED.
To view the rest of our Library and
download the REQUEST FORM, please
CLICK HERE
|
Carbon Monoxide
Carbon monoxide is a
deadly gas that is practically
colorless, odorless, tasteless, and
non-irritating. It is one of the
most common industrial hazards. An
estimated 10,000 persons seek
medical attention or miss at least
one day of normal activity each year
because of carbon monoxide
poisoning. Studies from the Center
for Disease Control indicate that
there are as many as 600 deaths
annually in the United States due to
carbon monoxide poisoning.
OSHA limits workers' exposure to no
more than 50 parts of carbon
monoxide per one million parts of
air (50 ppm) averaged over an
eight-hour workday. The seriousness
of exposure to carbon monoxide is
influenced by three main factors:
1. The concentration of carbon
monoxide in the environment,
2. The duration of the exposure, and
3. The exposed person's breathing
rate.
Harmful levels of carbon monoxide
are a danger to anyone who works
around equipment that produces it.
However, there are greater
occupational risks if you work in or
around warehouses, boiler rooms,
blast furnaces, diesel engines,
docks, garages, mines, petroleum
refineries, toll booths, or tunnels.
People who work with acetylene, pulp
and paper, or carbon black are also
particularly at risk.
Carbon monoxide poisoning produces
symptoms ranging from headache,
dizziness, disorientation, troubled
thinking, and abnormal reflexes to
coma and even death. Because the
symptoms of carbon monoxide
poisoning are so similar to the flu,
many people mistake them for the flu
or are misdiagnosed and are never
treated. Situations like these can
lead to serious problems, even
death, so it is important to take
the threat of carbon monoxide
poisoning seriously.
|
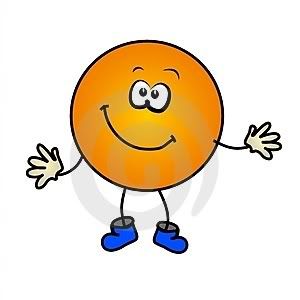
What's in
Your Wallet or Attitude?
By Michael Nance
I want to start by thanking everyone who
has graciously allowed me to be a part
of your accident prevention programs. This year has been very challenging to
all of us; gas price surges, economy
worries (both business and home), stock
market ups and downs, and the
elections. With more holiday
celebrations just around the corner I
hope that you and your families will be
safe in all that you do. For some, it's
a time of multiple parties that involve
alcohol, so be responsible. Take note
of others that may be having too much. All alcohol has "drinkability."
Perhaps you're going to have a nice,
big, warm fire in the fireplace. Well,
that's great if you prepare properly. Remember to have a source of fresh air
and be careful to not introduce
dangerous fumes into your home. Keep
flammables away and of course, if you
have a decorated tree it should be as
far as possible from the heat. Remember
to check for items on the mantle. Don't
forget like I did one year,...the
candles that were up there. They didn't
melt all the way, just leaned way over
as if taking a nap. My wife was not
happy. If you're using that chain saw to
prepare the wood, always use the correct PPE such as chaps, safety glasses, face
shield, hearing protection, and safety
boots. Watch out for bystanders. (Not
too mention those pesky spiders)
During this past year, we've all been
reminded about "safety attitudes." It's
one of the building blocks of a
successful program in the workplace. But it doesn't have to stop there.
Consider these ideas for creating,
changing, and uplifting attitudes over
the holidays. You've heard the phrase
"What's in your wallet?" well, what's in
your attitude. These can be with a
group or alone:
1) Visit a local nursing home. Maybe someone who can play the guitar
can do a few tunes, someone can read a
short story, etc. Make some treat bags
and ask the residents to share a
favorite holiday memory or share yours
with them. Organize these visits during
an extended lunch period. If you have a
Polaroid, take a group photo with the
resident and leave it with them so they
can brag about it. They will.
2) Send a hand written letter with
the card to people you haven't talked to
in a while, or maybe to some troops
overseas. Perhaps a small gift pack to
several members of the military.
3) Get a food drive started or help
one that is already established in the
work place. Think about the impact if a
company with 300 folks brought in 4
cans. Wow, that would sure help out and
it's not much more than the change in
the ashtray to each person.
If gift giving is part of your
celebration, think about the person(s)
that have everything already or that is
very hard to shop for. A good first aid
kit, fire extinguisher, disposable
camera, and a roll of duct tape make a
perfect "Safety" gift. Sure, you might
get some, Oh,.....<pause>......that's
"nice" feedback, but they'll remember
who gave it to them the first time they
really need it. For under $40 bucks
too.
Since gas prices have began to fall,
many of us may be considering taking a
few "road trips." Remember to practice
defensive driving and take some
preventative measures in the maintenance
of your vehicle. Sure we'll change the
oil, clean the windshield and vacuum the
interior, but what about the air
pressure check of the tires? For that
matter, how about the tires themselves? Contrary to popular belief, you can't
judge a tire by its cover. Most
automotive experts agree that along with
tread depth and proper tire maintenance,
tire age is also crucial to your safety
on the road. A cryptic code of four
numbers at the end of the 12-digit DOT
serial number can tell the consumer
which week and year a tire was
manufactured. Can you tell when your
tires were made? Tires made in the 1990s
have three numbers at the end of the DOT
code, while tires made after 2000 have
four numbers. For example, if the four
numbers are "3104," then the tire was
made during the 31st week of 2004. If
you happen to have old tires (made prior
to 2000), and the three digits are
"467," the 46th week of 1997. So the
next time you buy "new" tires, ask to
see them first and inspect the DOT
code. You don't want to buy new "old"
tires. Aged tires have a higher
potential for tragic tread separations.
Again, many sincere thanks to the
thousands of North Carolina employers
and employees that have participated in
NC Industrial Commission's Safety
Section accident prevention programs. We are developing new topics and
programs that you have requested and
look forward to serving you in 2009 and
beyond. Remember, we are working for
you!
Editor's note: Michael Nance is the NCIC
Blue Ridge, Southern & Western Piedmont
areas Safety Representative. If you are
interested in having one of our programs
in your area, please give Michael a call
at 919-218-9047 or email him at
Michael.Nance@ic.nc.gov
|
Grounded
By
Mike Bingham
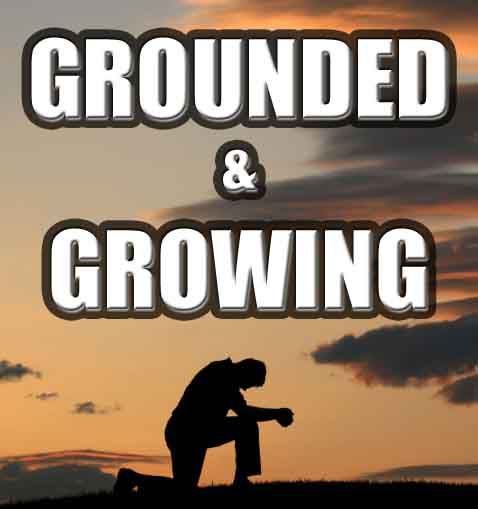
It used to be that the
word "grounded" struck fear and dread
into my very heart. The word usually
followed my being caught in some sort of
mischief when I was a kid, like the time
I wired up three small light bulbs in
what I thought was a parallel circuit. I wired in a knife switch, explained the
whole thing to Dad, and after he
reluctantly gave me permission to plug
it in I closed the switch and watched
the bulbs explode and bounce glass off
the ceiling. The arc flash was small but
impressive, but Dad wasn't amused. He
made me dismantle the apparatus and
pronounced the dreaded word - grounded.
Many years later I came to understand
parallel circuits, series circuits,
voltage ratings (wonder what the three
exploding bulbs were rated...), and the
term grounded took on a different
meaning. Today hearing the words, "not
grounded" can cause me fear and dread
just as "grounded" did in days of old.
With electricity current will flow from
a source, through a load, and back to
the source. Remove the load and no
current will flow. Remove a wire going
to or from a load and again no current
will flow. The source uses the earth as
ground, so an energized wire will let
current flow through it to a load and
back to the grounded end of the source.
The source, load and wires are called a
circuit.
If you use a power tool or piece of
equipment with a metal frame or cover,
everything is safe to touch as long as
the current follows the intended path
through the equipment. An electric
heater with a metal housing is an
example. If the current flows through
the wire to the heating elements and
back to the source, and doesn't flow
anywhere else, you could safely touch
the heater's housing whenever you
wanted. But if the wire gets frayed and
touches the heater's metal housing, and
you were to touch it, then you would
likely receive a shock if you were
touching earth ground or objects
connected to earth ground because you
would become a wire yourself, diverting
some of the current to ground.
One good safety measure is to use tools
and equipment that are either double
insulated or have three-conductor cords
with ground prongs that are intact. The
ground wire in the three-conductor cord
connects to the metal body of the device
and provides a path to ground for
current that gets out of bounds, so to
speak, and could cause a user to get
shocked were it not for the ground wire.
Equipment grounds must be checked and
maintained in order to have maximum
safety benefit. One way to check
grounds is to use an ohm meter to verify
that the ground wire has continuity from
the ground prong on the cord to the body
of the device. There are AC sensors
available that you can touch a device
with to verify the ground. If the
sensor lights up when you touch it to
the device in question, the ground is
missing. What if the ground prong is
present and the ohm meter shows
continuity but the sensor lights up? It
could be that the receptacle is
defective. You can buy a receptacle
tension tester to use as part of your
ground maintenance program. Receptacles
do eventually wear out. If the tension
tester says everything is OK but your AC
sensor shows a problem, there could be a
broken or disconnected wire in the
circuit - a problem that must be
corrected.
Always verify that each instrument you
use is working correctly and follow its
manufacturer's instructions. Consider
setting up a preventive maintenance task
and schedule regular ground testing to
ensure no one is hurt or killed by such
a simple thing.
If you aren't sure how to do proper
ground tests, consider having a licensed
electrician come into your facility and
do the testing for you.
Editor's Note: Mike Bingham is the Western Area Safety
Representative for the NCIC, and one of
the 10 members of the NCIC's Safety
Department who are out there Working
for You!!!to make N.C. workplaces
safer and better by reducing injuries to
employees and saving money for employers
through education and training. You can
contact Mike at:
mike.bingham@ic.nc.us or call:
919.218.9045
|
From the Desk of
Dennis Parnell
Director Safety Education
Inspiring Others?
Being a mentor can be challenging, but
studies have shown that it can be as
rewarding for the mentor as for those on
the receiving end. To be a successful
mentor:
See others' strengths - One of the main
purposes of a mentor is to help others
feel up to the task of whatever they are
expected to do. You must be able to see
other people's strengths and understand
how they can be best put to use,
remembering that there is always more
than one way to accomplish a task.
Set high standards - Quite often, people
aren't aware of how much they are
capable of achieving. Challenges alone
can motivate some people, and setting
high standards can help to keep people
interested.
Be receptive and available - If you set
high standards, but you aren't available
when mentees start to feel overwhelmed,
challenges are likely to have a negative
affect. When you're available to coach
and listen to your charges, however,
challenges may start to seem more
achievable.
If you haven't considered being a mentor
to someone, you just might want to think
about doing it. You can make a
difference!
Now you know. Dennis :)
|
Insight!
Fun and useless tidbits
Unusual
Celebrity Deaths:
Duane Allman - musician
1971 --- motorcycle accident.
Attila the Hun
453 AD --- bled to death from a
nosebleed on his wedding night.
Lucille Desiree Ball
1989 --- died after undergoing heart
surgery.
Velma (Margie) Barfield
1984 --- 1st woman executed in US since
restoration of death penalty in 1967.
(For poisoning her fiancée.)
Marie Curie - chemist, discovered
Radium
1934 --- leukemia, caused by exposure to
radiation.
_______________________________________________________
Martha
Washington-1902 --- 1st woman to
be pictured on a US postage stamp. The
8-cent stamp was issued in November
1902.
.
Carlos Santana-1998 --- 1st
Hispanic to be inducted into the
Rock and Roll Hall of Fame.
|
Why do we procrastinate?
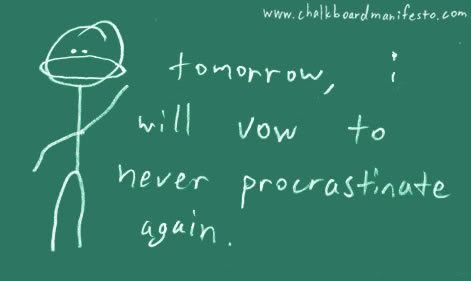
About 20 percent of people make a habit
of procrastinating, and for some, it
results in missed opportunities, late
fees, and blown deadlines. There are
three major reasons that people
procrastinate:
1.
Theythrive on excitement and the
adrenaline rush they get when they must
hurry to meet a deadline.
2. They
are overwhelmed or cannot make a
decision about how to proceed.
3. They
fear failure.
Individuals may also have very personal
reasons for putting things off. For
example, someone who has trouble
accepting authority might attempt to
postpone those tasks which have been
assigned by superiors. Likewise, someone
who is depressed might struggle with his
energy levels and therefore find it
difficult to get started on a project.
If you
are a procrastinator, you might think
that putting things off is a harmless
personal choice, and while it is a
personal choice, it may not be harmless.
By procrastinating, you put added
pressure on yourself, and the kind of
stress this generates can weaken your
immune system, potentially leading to
more frequent illness.
Procrastination can also hinder teamwork
by making it difficult for team members
to trust that work will get completed,
and often puts an unfair burden on those
who do not procrastinate.
For some
people, acknowledging the reason they
procrastinate is helpful to curb the
behavior. For example, if you realize
that a project overwhelms you, it may be
possible to break it down into
manageable pieces. If you fear failure,
realize that putting off the work not
only has the effect of increasing your
fear, but cuts down on the time you have
to ensure the project is a success.
|
What Folks
Are Saying
Mel,
Thank you so much for the Defensive
Driving class. Everyone enjoyed and
received a lot of good information from
the class.
It was nice to see you again and I hope
to see you again in the future.
Thank you again,
Glenda Hollowell
Colony Tire
________________________________________________________
Dennis,
As we are
wrapping another successful year of
Safety Training. I felt that it should
be brought to your attention what an
impact Mike Bingham has contributed to
Henderson County's bottom line. Mike is
a top notch professional that truly puts
his heart and soul into what he does. Mike is an extremely knowledgeable
professional that has contributed to
Henderson County's 50% reduction in
Workers Compensation claims over the
last 2 years, with an approximant cost
savings of $196,000 in Actual Workers
Compensation claims costs. He really
connects with our staff from regular
employees to Department Heads. In
addition to providing the required
training per OSHA, he provides job
specific training that fits Henderson
County's needs. Mike adds such a
magnificent flare to his training
sessions he continues to maintain the
employees interest training classes
after training class. In fact the
attendance for Safety training continues
to increase. Mike continues to be a
role model for me and my career as Risk
Manager for Henderson County. I feel so
fortunate to have a resource on many
Risk Management questions that I have. The amount of time Mike saves me with
training and providing me with valuable
answers to questions that I may have
truly has freed me to provide a better
service to Henderson County employees
and citizens. This I feel has
contributed to additional savings from
Henderson County not having to hire a
service to provide our training. Mike is
not just someone we look at as our
Safety Trainer he is part of our TEAM.
I can honestly
say on behalf of the employees and me
that we look forward to another
outstanding Safety Training year with
Mike being a major contributor with our
new successes.
Sincerely,
Yvonne Moebs,
Risk Manager
Henderson County,
NC
______________________________________________________
Dennis:
I would like to let you and your crew
just how much I enjoyed last month's
training. That was probably one of the
most informative and helpful training
sessions I've attended in my 27 ½ yrs.
of State service. You all are to be
commended. Being funny and positive
really helped to make the days
interesting and kept a lot of us older
folks, lol, from falling asleep. Keep
up the good work and I look forward to
seeing you all again next October in
Asheboro.
Capt. Marilyn Jean Martin
.
|
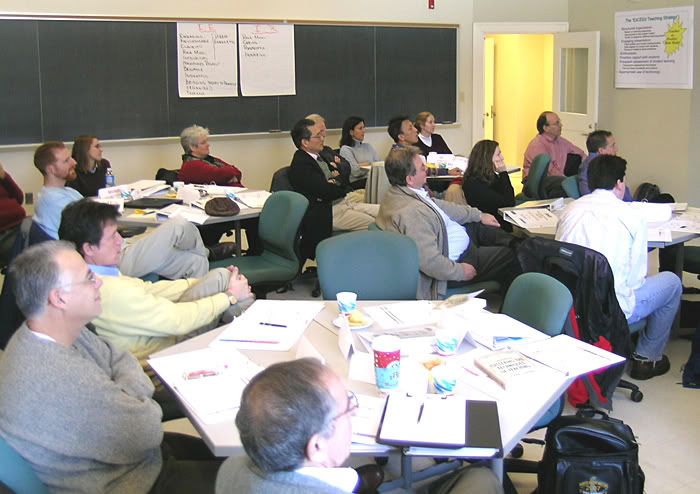
Advanced Accident Prevention
Certificate Awareness Program Coming
in 2009
The North Carolina Industrial
Commission's (NCIC) Safety Education
Section is wrapping up the development
phase of its new Advanced Accident
Prevention Certificate Awareness Program
(APCAP). This new class is a two-day
event offered only to persons who have
completed any one of the original
30-Hour APCAP classes that have been
offered throughout the state over the
past two years. It will build on some
of the topics covered in the original
30-Hour and will add some new subjects.
Subject matter is intended to assist
people with workplace safety
responsibilities in reducing work
related injuries and illnesses by
building on concepts presented in the
original 30- hour APCAP.
The first session in the course will
be,
"Project Management for Safety
Folks." This class will
cover basic project management
techniques and will provide a
foundation for the rest of the
sessions in addition to providing a
durable tool that can be used over
and over again not only in safety,
but in many other business
activities as well.
The next session will be a class
titled,
"Worker's Comp How To." It
will be presented by seasoned
Worker's Comp personnel from the
NCIC and will provide an excellent
opportunity to get information
straight from the source.
"Body Mapping for Ergonomics"
will build on the Ergonomics class
taught in the original 30-Hour
sessions. It will provide a fun,
unique method of identifying and
fixing ergonomic issues.
"Safety and Health Audits"
will be the next class and will
expand upon the 30-Hour APCAP class
"Safety and Health Programs." The
activities will include discussing
written plans and comparing them to
the real world of the shop floor. Gap analysis will be covered.
On the heels of "Safety and Health
Audits', the next topic will be
"Observation-based Safety and Health
Audits." Participants will
use a Job Hazard Analysis (JHA) from
their workplace to identify which
behaviors are critical to ensuring
safety. Discussion on how to
conduct observations will be a big
part of this session. Previous
30-Hour APCAP classes taught JHA,
and the Observation-based S&H class
will put that knowledge to use.
The first day will conclude with
"Recognition Programs." In
this class participants will use a
template supplied by the NCIC to
fill out a sample written plan that
can be taken back to their
workplaces and submitted for
approval.
The second day will begin with
"Safety Committees," a class
on roles and responsibilities of a
safety committee. Training and
motivating the safety committee will
be included as well.
The participants will move into the
"Safety Math" class
which is a basic overview of common
metrics used by employers and safety
personnel. Things learned here will
carry over into the next class,
"Selling Safety to Management."
Up next is
"Safety Rules." In this
session participants will submit
their sites' safety rules to the
instructors who will review them and
help fill out an application for
acceptance into a potential
money-saving program related to the
NC General Statutes 97-12 rule. If
applicable, site visits can be
scheduled for companies who want to
take advantage of this program.
The last class of the event will be
"Contractor Safety," wherein
participants will fill in a
contractor safety sample plan with
their own site's information and
have a second document ready to
submit to their management for
approval. Certificates will be
awarded at the end of the second
day, concluding the class.
We will be posting
registration information in December!
|
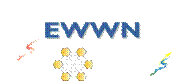
E astern
Water/Wastewater Workshop
December 17, 2008
Please join us for the Eastern Water &
Wastewater Six (6) hour Workshop to be
held in Tyrrell County.
Date: Wednesday, December 17, 2008
INSTRUCTORS: NC INDUSTRIAL COMMISSION
-
ERIC JOHNSON
-
DENNIS PARNELL
Topics are as follows:
- Working in Cold
Conditions
Location: Tyrrell Hall(Across from Hess/Wilco
station)
906 Hwy
64 East
Columbia,N.C.
Registration at 7:45 AM
Classes
begin at 8:00 AM-4:00 PM
Refreshments at the breaks and lunch
will be provided by the Eastern Water &
Wastewater Network.
Cost for
the workshop will be $15.00.
For
additional information and registration,
call or email
PARKER NEWBERN
at
252-331-3044.
|
Extension
Cords and Holiday Lighting
By Randy Cranfill
With the holidays
approaching, lights and decorations will
soon be showing up in homes and
businesses across the country.
Electrical extension cords will
frequently be used to supply electricity
to these lights. Most people never check
their extension cords before they use
them, but they can cause electrocution,
burns, serious shock, and fires.
The U.S. Consumer Product Safety
Commission estimates that about 3,300
residential fires originate in extension
cords each year, killing 50 people and
injuring about 270 others. The most
frequent causes of such fires are short
circuits, overloading, damage, and/or
misuse of extension cords.
These hazards can be prevented by
following these important safety tips:
1. Visually check each cord and lights
to make sure they are in good condition.
2. Check for cracking and fraying for
these are indications that they needs to
be replaced.
3. If the cord feels hot unplug and
replace the cord.
4. Keep all outdoor extension cords and
light strands clear of wet conditions.
5. Never use outdoor extension cords,
lights and electric decorations that are
not protected by GFCIs.
6. Avoid running extension cords and
light strands through doors and windows.
7. Never run extension cords under
furniture, carpeting, or behind
baseboards for they can present a fire
hazard.
8. Do not place extension cords across
walkways for they can cause people to
trip and fall.
9. Unplug all holiday lighting before
leaving home or going to sleep.
10. Don't let children play with
extension cords, light, and electric
decorations.
Please take a few minutes to help make
your holidays a safe one.
|
It's
that time of the year! Holidays, family
time, lots of food, and sometimes an
unwanted visitor!
Foodborne Illnesses and how to avoid
them.
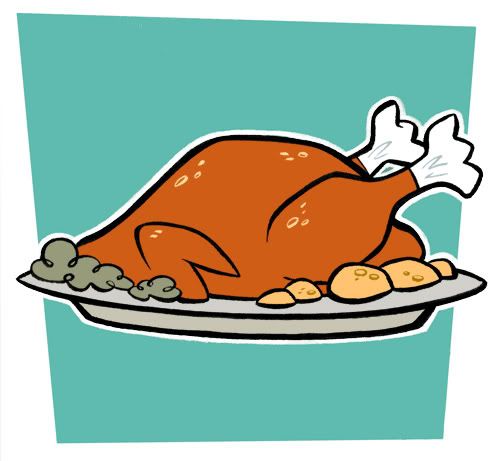
By: Eric Johnson
Background:
It is estimated that 76,000 illnesses,
325,000 hospitalizations, and 5,000
deaths in the United States each year
can be traced to the food we eat. More
than 250 known diseases are contracted
through food contaminated by bacteria,
viruses, parasites, toxins, metals, and
prions. Foodborne-disease outbreaks (FBDOs)
happen every year, sometimes affecting
multiple states and many people, which
can be traced back to of variety of food
items.
For example, during the months of
September and October in 2006 two FBDOs
occurred that could be traced to fresh
produce. The first, caused by a bacteria
called Escherichia coliform (E.Coli),
infected approximately 200 people in 26
states from California to Maine. This
outbreak was traced back to
contamination of fresh spinach.
Additionally, during those two months in
2006, a bacteria called Salmonella was
implicated in a tomato contamination
that affected 183 individuals in 21
states. Back in 1985 a large isolated
outbreak, caused by the pathogen
Clostridium perfringens (C. perfringens),
occurred in Connecticut after a group of
factory workers enjoyed their employee
banquet. The culprit causing this
outbreak, which affected approximately
600 employees, was determined to have
been the gravy, which had been
improperly cooled and then reheated
prior to being served at the banquet.
These three bacteria, E. Coli,
Salmonella, and C. perfringens,
represent some of the most common causes
of foodborne illness. These illnesses
are easily diagnosed due to tests that
allow for the detection of the pathogen
in a person's system. Additional
information regarding these bacteria is
included as follows:
E. coli:
This bacteria is carried in
cattle or similar animals. Illness from
this bacteria is caused by consumption
of food or water contaminated by small
amounts of feces. The symptoms resulting
from this infection include severe and
bloody diarrhea and painful abdominal
cramps. 3-5% of cases lead to hemolytic
uremic syndrome that can lead to
temporary anemia, profuse bleeding, and
kidney failure.
Salmonella: This is a bacteria
carried in the intestines of birds,
reptiles and mammals. It is contracted
by ingesting a variety of different
foods from animal origin. The symptoms
resulting from infection by this
bacteria include fever, diarrhea, and
abdominal cramps.
C.
perfringens: This is a rod-shaped
bacteria that lives in environments that
do not contain oxygen, such as in the
intestines of humans and domesticated
animals. These bacteria produce spores
that exist in soil, sediment, and areas
prone to human or animal fecal
pollution. The symptoms resulting from
infection by this bacteria include
abdominal cramps and diarrhea that
usually resolve in 1 to 2 days.
Ingesting large numbers of this bacteria
could lead to necrotic enteritis,
leading to severe damage to the
intestines, which can be fatal.
As stated before, illnesses caused by
these pathogens can be definitively
diagnosed due to tests that can detect
the pathogen in a person's system or in
the food that was consumed. However,
many foodborne illnesses are caused by
pathogens that cannot be detected or
have not been identified, thus these
sicknesses remain undiagnosed. In fact,
nearly 82% of illnesses and
hospitalizations, and approximately 64%
of deaths caused by foodborne illness
each year remain undiagnosed.
This inability to diagnose many of the
illnesses caused by our food has led to
complication in detecting when FBDOs are
occurring in the population.
Additionally, although some foodborne
diseases cause extreme symptoms such as
kidney failure, paralysis, or even
death, many cause common flu-like
symptoms such as vomiting and fever.
Because of this, many cases of foodborne
illness simply go unreported. The
Centers for Disease Control and
Prevention (CDC) has instituted
procedures that aid in the surveillance
of foodborne illnesses in order to
determine and act upon any FBDOs that
may occur.
The CDC has defined a FBDO as the
occurrence of two or more cases of a
similar illness resulting from the
ingestion of a common food. The ability
to monitor FBDOs has steadily become
more effective in recent years due to
the electronic Foodborne Outbreak
Reporting System (eFORS). This
electronic database allows local, state,
territorial, and federal health agencies
to report food-borne illness cases as
they happen. The CDC then monitors this
database and performs any investigations
needed into multiple cases of the same
illness, or patterns of illness in the
population. This database has made it
possible to react to FBDOs that may be
occurring within the population quickly
and effectively, maximizing the ability
of health care providers to treat those
that have been affected and increasing
the safety and awareness of consumers.
Prevention
Although strides have been made to cope
with FBDOs as they happen, there are a
few simple habits that you can
personally do that significantly
decrease your chances of contracting a
foodborne illness. When purchasing,
transporting, storing and preparing food
there are measures that should be taken
in order to ensure the safety of the
food you are consuming. Many foodborne
illnesses arise out of carelessness in
the handling of our food prior to
consumption. The following is a list of
practices that can be followed to
minimize the likeliness of contracting a
foodborne disease.
Choosing
the Right Food at the Right Time:
When shopping, get canned and
packaged foods first before heading
to the refrigerated sections of the
grocery store. Make sure cans are
not bulging or dented. Check for
cracks in jars and avoid jars with
bulging lids. If canned or packaged
goods are sticky on the outside this
could indicate a leak, and these
products should be avoided.
Choose pasteurized milks and
cheeses, as well as juices and
ciders that have been pasteurized or
treated. Pasteurization is
accomplished by significantly
elevating the temperature of the
product during processing, thus
killing any microorganisms that may
cause illness.
Select eggs that are refrigerated
and check the eggs, before leaving
the store, for any cracks. Cracks
can allow microorganisms to enter
the eggs, thus increasing the
chances for illness.
Wait to select frozen food and
perishables, such as meat, poultry,
and seafood, until the end of your
shopping trip, and bag these
products separately in plastic bags
so the drippings do not contaminate
other food in the shopping cart.
Bring a cooler full of ice to keep
frozen and perishable foods cold if
your return trip from the grocery
store will be longer than one hour.
Storage:
Refrigerate (40°F) or freeze (0°F)
perishables immediately upon arrival
home from the store.
Store eggs in carton in the
refrigerator. Avoid storing them in
the door because the temperature is
warmer here due to the door being
opened and closed.
Meats, poultry and fish can be
placed in the refrigerator in the
packaging from the grocery story if
they are to be cooked within 1-2
days. For longer storage, these
items should be wrapped tightly and
placed in the freezer.
Preparation:
Produce should be cleaned prior to
preparation in order to remove any
dirt and grime. Pay special
attention to cleaning produce that
will be eaten raw because there will
be no heat involved during
preparation to kill lingering
bacteria.
Wash hands, utensils and cutting
boards that have come in contact
with meat or poultry before
preparing other foods. This reduces
the possibility of cross
contamination.
Cook meat, poultry and eggs
thoroughly. Ground beef should reach
an internal temperature of 160°F,
and eggs should be cooked until the
yolk is firm.
Make sure to refrigerate any
leftovers promptly so contamination
is not allowed to occur.
These prevention measures are needed to
limit the possibility of contamination
of our food as it travels from the farm
to our tables. However, if contamination
does occur, and a foodborne illness
results, it is important to report this
to your local health department. With
the information you provide, health
officials can gain a better
understanding regarding the
initialization, transmission, and other
contributing factors to FBDOs.
Sources
for More Information
For more information please visit:
The Centers for Disease Control and
Prevention FBDO toolkit
http://www.cdc.gov/foodborneoutbreaks/toolkit.htm
The U.S. Food and Drug Administration
Info on Foodborne Illness
http://www.cfsan.fda.gov/~mow/foodborn.html
Eric Johnson is the Mid-State Safety
Representative and Water/Wastewater
Coordinator and covers a fourteen county
area around Raleigh. Please call
919-218-3567 to schedule training.
Eric
Johnson is the Mid-State Safety
Representative and Water/Wastewater
Coordinator and covers a fourteen county
area around Raleigh. Please call
919-218-3567 to schedule training.
|
|
About NC Industrial Commission
Safety Section
The NC Industrial
Commission Safety Education Section
stands ready to assist you with your
Safety training needs. We offer a
variety of courses, designed to suit
your needs. Please give one of our
Industrial Safety Representatives a
call.
DENNIS
PARNELL
Director Safety Education
919-218-3000-Cell
919-807-2602
Dennis.Parnell@ic.nc.gov
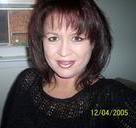 KIM
NADEAU
Program Assistant
919-807-2603
919-218-9049-Cell
Kim.Nadeau@ic.nc.gov
RANDY
CRANFILL
APCAP & APW Coordinator
919-218-2986
Randy.Cranfill@ic.nc.gov
ALVIN
SCOTT
Eastern & Northeastern Areas, Eastern
Defensive Driving Instructor
919-218-2792
Alvin.Scott@ic.nc.gov
WE ARE WORKING FOR YOU!
|
|
|
Quick Links
May 12 - 15, 2009
EXHIBITORS!
|
Quick Links
NCIC HOMEPAGE IN SPANISH
CLICK
BELOW TO VIEW OUR HOMEPAGE IN SPANISH
READ MORE...
|
Quick Links
Rate of Worker Injuries Fall in North Carolina
|
Quick Links
Construction
Contractors Jobsite Checklist
|
Quick Links
General
Industry
A Review
of HAZCOM
|
Quick Links
Fleet Safety
Courtesy & Safe Driving
|
Quick Links
SIGN-UP FOR OUR
Email/Newsletter
|
Quick Links
Click below for a Merry Christmas greeting
from the Safety Section Staff
|
Quick Links
NC RURAL WATER ASSOCIATION
|
Quick Links
CENTRAL
PIEDMONT SAFETY COUNCIL
Membership Brochure
|
Quick Links
EASTERN
CAROLINA SAFETY COUNCIL
Membership Brochure
|
Quick Links
SOUTHEASTERN SAFETY COUNCIL
Membership Brochure
|
Quick Links
WESTERN PIEDMONT SAFETY COUNCIL
Membership Brochure
|
Quick Links
MID-STATE
SAFETY COUNCIL
Membership Brochure
|
Quick Links
BLUE RIDGE SAFETY COUNCIL
Membership Brochure
|
Quick Links
NORTHEASTERN SAFETY COUNCIL
Membership Brochure
|
Quick Links
WESTERN CAROLINA SAFETY COUNCIL
Membership Brochure
|
|