Greetings Friends in
the Name of Safety:
It's hard to believe that Thanksgiving
is almost here! The older we get, the
quicker time seems to go by. As we take
time to reflect on the many things we
have to be thankful for, i.e. family,
friends, home, jobs, etc., let's not
forget those who are less fortunate.
We at the NCIC Safety Section are
sincerely grateful for YOU, our many
friends across this great state! We have
hosted around nine 30-hour Accident
Prevention Certificate Awareness
Programs this year with several hundred
participants. This program began in
March of 2006 in Clemmons, NC. We could
not foresee the success that this
program would achieve. Time and time
again, you tell us how this program has
helped you with your goal of growing
your Accident Prevention Program in your
workplace. Our only mission is to assist
you in accident prevention and we thank
each of you and your employer for your
continued support.
Currently, we are trying to finalize our
2009 APCAP schedule. We will be adding
an
ADVANCED APCAP in 2009. In order
to participate, you must have completed
the basic 30-hour APCAP. The ADVANCED
APCAP will be two days of intense
training to further assist you with your
Safety & Health program.
In 2009, we will offer
BOTH
COURSES concurrently on the same
date and location in order to better
serve you.
Here are
the "PROPOSED" DATES AND LOCATIONS for
2009:
-
February 9-14, 2009—Wilmington, NC
- March
23-27, 2009—Roanoke Rapids, NC
- June
15-19, 2009—Smithfield, NC
- August
17-21, 2009—Flat Rock, NC
-
September 14-18, 2009—Atlantic
Beach, NC
-
October 26-30, 2009—Asheboro Zoo,
Asheboro, NC
We look forward to seeing you at one of
our programs in 2009. Again, let us say
"THANK YOU" for allowing us to be a part
of your family.
Your
REGIONAL SAFETY COUNCILS are
continuing to work for you, so please
refer to the calendar section of our
Safety Bulletin for more information.
Please support YOUR councils!
As always, we thank you for your support
and we pledge to continue to serve your
needs. We promise to continue to provide
quality
ACCIDENT PREVENTION training
programs.
|
Is it a cold
or is it the flu?
Cold and flu season is upon us, and
unfortunately the two illnesses share
more than a season—they share symptoms.
In fact, the two ailments are so similar
that it is often quite difficult to
determine which one you have, and in
many cases, it's important to do so. The
flu, if not properly treated, has the
potential to turn into a much more
serious illness like sinusitis or
pneumonia.
Though a cold can make a person quite
miserable, it rarely comes with a fever
of more than 101 degrees, and often goes
away on its own within a week. A sore
throat and a stuffy nose are common
symptoms with a cold. Flu, however,
often comes on more suddenly and comes
with more severe symptoms. A high fever
and extreme exhaustion are common with
the flu. Even if you think you can tough
it out, severe or persistent symptoms
(like a prolonged high fever or frequent
vomiting) merit a doctor's visit to
determine the best course of treatment.
To ward off illness altogether, wash
your hands frequently, get plenty of
rest and exercise, and eat a
well-balanced diet. You might also want
to consider getting a flu shot if you
haven't already.
Also, don't forget to get your flu shot!
|
Thanksgiving food poisoning not
so festive!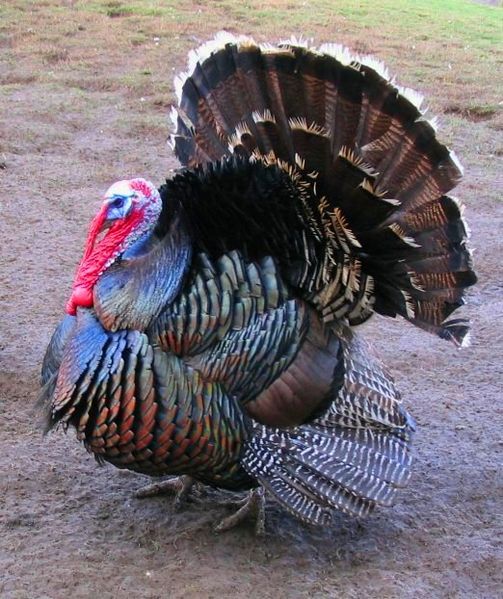
The holiday season is approaching, and
while some people look forward to
holiday parties and family gatherings,
many people most look forward to a
perpetual spread of festive recipes and
treats. Unfortunately, while you
probably know that the holiday season
can be rough on your waistline, you
might not realize that it's also a prime
season for food poisoning.
The Centers for Disease Control (CDC)
estimates that there are 76 million
cases of food poisoning in the United
States each year. Fortunately, there are
safe ways to handle food that can keep
you and your guests from getting sick.
1.
Wash
your hands frequently—Using
soap and warm water, wash your hands
both before and after preparing and
handling food, especially raw meat or
poultry.
2. Prevent cross-contamination—Keep
raw meat and poultry from touching or
dripping on other foods. Cross
contamination can also occur when
surfaces are not properly sanitized
after use.
3. Cook foods thoroughly—Meat and
eggs can be particularly dangerous when
they are not cooked thoroughly. For
maximum safety, eggs should be cooked
until firm (not runny) and meat and
poultry should be cooked until juices
run clear.
4. Store food properly—Perishable
food should be refrigerated or frozen
when not in use. Use the microwave or
the refrigerator to thaw frozen foods
instead of allowing them to sit out.
Many foods are prepared specially for
the holiday season, and sometimes a
cook's unfamiliarity with ingredients
and recipes is at the root of unsafe
practices in the kitchen. Remember:
- Turkeys should be defrosted in
the refrigerator, not on the counter (at
room temperature). Slice leftovers into
serving-sized portions before storing in
the refrigerator—an entire bird may be
too large to store safely.
- Stuffing cooked inside a turkey
is more susceptible to bacteria. Stuff
your turkey only after it is cooked
through and prepare turkey and stuffing
separately.
- Eggs—Especially in homemade
eggnog, ensure that eggs are cooked at
160 degrees before they are consumed.
- Buffets—The
longer food is left out, especially
after two hours, the higher the risk of
food poisoning. Store food as soon as
your guests are done eating.
Food poisoning usually strikes between
two and four hours after eating
contaminated foods and is most dangerous
for the elderly and children under six.
Symptoms—which are similar to the flu
and include nausea, vomiting, diarrhea,
fever, headaches, and weakness—can last
up to 10 days.
|
Shh...Listen!
Leaders that means you too!
Many
people assume
that in a group situation, leaders
should do all the talking. The reality,
however, is that leaders need to be
equally as capable of listening—but it's
harder than it sounds.
1.
Give undivided attention. It's
not worth listening to someone's
feedback or opinion if you're not
willing to stop what you're doing and
look someone in the eye. If you don't
have time to truly give your full
attention, schedule another time to
chat.
2.
Prove it. Provide the speaker
with clues to show that you are paying
attention. Nodding, smiling, and asking
questions will help people feel that you
are invested in what they have to say.
You're also likely to come away with a
better understanding of their point in
the end.
3. Empathize.
It sounds trite, but when was the last
time you really considered what
it might be like to be in someone else's
shoes? Try it, and you might gain new
insight on a situation.
4. Wait your turn.
Interrupting or changing the subject
sends the message that what you have to
say is more important than what someone
else is offering. Give people time to
express their views before expressing
yours..
|
NCIC Video Library
Check out our
Video Library !
Almost there! We
are in the process of UPDATING our
online Video/DVD listings. Please be
patient with us.
To view the rest of our Library and
download the REQUEST FORM, please
CLICK HERE
|
Get To Know Your Deputy
Commissioners
Chief Deputy Commissioner
Stephen T. Gheen
On December 20, 2005, pursuant to the
revision of N.C. Gen. Stat. §97-78 by
the 2005 General Assembly, Chairman Buck
Lattimore officially named Stephen T.
Gheen as Chief Deputy Commissioner of
the N.C. Industrial Commission. Mr.
Gheen was an Assistant Attorney General
before he joined the the Industrial
Commission on August 1, 2000, as a
Deputy Commissioner. At that time,
Chairman Lattimore designated Mr. Gheen
as the "lead worker" for the Deputy
Commissioner section, with the working
title of "Chief Deputy Commissioner."
Steve Gheen graduated from Western
Carolina University with a B.A. degree
in 1972 and an M.A. degree in History in
1974. He received his J.D. from North
Carolina Central University in 1985.
He has served as a Deputy Commissioner
of Insurance; Clerk to the Honorable
Hugh A. Wells (deceased), Judge of the
North Carolina Court of Appeals;
Assistant District Attorney for Judicial
District 27-A; in the private practice
of law in Gaston County for 13 years;
and Assistant Attorney General of the
N.C. Department of Justice, assigned to
the Industrial Commission as agency
counsel.
Mr. Gheen is a native of Cleveland
County, is the father of two children,
and is married to Cathy Moore, an
attorney for the County of Durham.
To e-mail Chief Deputy Commissioner
Gheen
CLICK HERE
|
NFPA
releases 2009 Edition of NFPA 70E®
By W. Jon Wallace, CSP, MBA:
Workplace Group

The National Fire Protection
Association (NFPA) issued the
revised 2009 edition of NFPA 70E®:
Standard for Electrical Safety in
the Workplace with an effective date
of September 5, 2008. The 2009
edition of NFPA 70E® contains
numerous revisions. Listed below is
a summary of the major changes:
·Contractor Relationships: Article
110.5 requires host employers inform
contractors of known hazards covered
by NFPA 70E® related to the contract
employer's work. The contract
employer shall ensure that each of
his/her employees is instructed in
the hazards provided by the
employer.
·Training Requirements—Emergency
Procedures: Article 110.6 requires
employees exposed to shock hazards
that are not reduced to a safe level
by applicable electrical
installation requirements be trained
in approved methods of
resuscitation, including
cardiopulmonary resuscitation (CPR).
The training shall be certified
annually by the employer.
·Electrical Safety Program Audit:
Article 110.7 requires the written
electrical safety program be audited
on a frequency established by the
employer.
·Arc Flash Hazard Analysis: Article
130.3 requires the arc flash hazard
analysis be updated whenever a major
modification or renovation takes
place. In addition, the analysis
shall be reviewed periodically, not
to exceed five years.
·Arc Flash Protection Boundary: The
criteria for the 4 feet arc flash
protection boundary for voltage
levels between 50 and 600 volts has
been modified based on upstream
protection device clearing time of
maximum 2 cycles (0.033 seconds) and
available bolted fault current of 50
kA or any combination not exceeding
100 kA cycles.
·Equipment Labeling: Article 130.3
(C) states equipment shall be field
marked with a label containing the
available incident energy or
required level of PPE.
·Selection of Personal Protective
Equipment: Article 130.7 contains
several revisions with respect to
arc flash PPE requirements. For
example: Table 130.7 (C)(9) has been
expanded to include additional job
tasks such as performing infrared
thermography as well as other
non-contact inspections outside the
restricted approach boundary.
Additional categories of equipment,
such as arc-resistant switchgear,
have been added to the revised
table. Also, Table 130.7 (C)(10) has
been revised and placed an a more
user-friendly format.
· Annex
Revisions: The following annexes
have been significantly
revised—Annex F (Hazard/Risk
Evaluation Procedure); Annex H
(Simplified, Two-Category,
Flame-Resistant [FR] Clothing
System.)
Please remember this article is
intended as an overview and not a
comprehensive summary of changes to
the 2009 edition of NFPA 70E®.
For more information on electrical
safe work practices click on this
link for our November 21, 2008
course:
CLICK HERE!
If you have any questions concerning
this article or other safety issues,
please contact W. Jon Wallace at
919.933.5548 or e-mail
to:
jwallace@workplacegroup.net
|
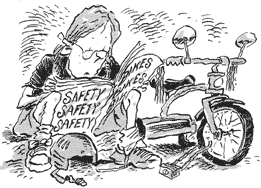
Safety
Attitudes Are Free!
By Michael Nance
Perhaps the election results will be known
by the time you read this, or maybe not.
I've said it several times in the past few
weeks; I'm not sure we'll know who is
elected President of the United States for a
few days after the election. It has been a
long hard fight for many politicians
including those that are local to North
Carolina. Some of the campaigns have spent
millions of dollars for the opportunity. I
can't help but think of how much money has
been raised in the process. Add to it the
revenues from the lottery and wow, that's a
lot of cash people have donated. More than
enough to cover the increase needed for the
state's budget don't you think? Yet, we all
are facing cutbacks and some of the folks I
know have already been told that their
company is closing or at least reducing the
employee head count.
Sadly, some folks will feel the need to trim
safety programs. After all, on the surface
it is money spent with limited return on
investment. However, just like most seasoned
investors will tell you, you must be in it
for the long haul. Before somebody gets
upset, I used the words "on the surface".
Safety programs will more than pay for
itself deep down. Fact is, safety is really
a free attitude. Take away the incentives,
the perks, and the give-aways and what do
you have? For a truly dedicated safety
program, you should still have employers and
employees willing to do what is right
regardless of who gets credit. You have a
strong sense of accountability for each
other and the reward of going home the same
way you came in. All the while saving
expenses for other critical business needs
because of a good safety program. Directly,
those savings coming from reduced or
insurance and injury costs. These savings
help carry organizations through tough times
or provide salary and wage increases, or
better tools to get the job done. The list
goes on.
All of us with the NCIC Safety Section meet
folks every day with the enthusiasm for
achieving an accident free workplace no
matter what. They understand what it means
to use our services, as well as others, to
keep safety in the forefront of every action
taken. It isn't easy. Using the NCIC Safety
Section directly saves you money. To be
successful it takes work! Sometimes more
than we thought, but aren't the rewards
sweeter when we've rolled up our sleeves and
tackled the hazards of the workplace with
the tools and knowledge gained from
listening to each other and simply being
involved with safety. I do a fair amount of
woodworking and I normally give my
brother-in-law something I've made from the
"ground up" for Christmas. Sure, I could go
buy it (sometimes cheaper), but it's much
more valuable and satisfying when I've
poured sweat into it and made it myself. I
protect it because I am proud of it. Sure I
make mistakes, but I didn't get hurt in the
process by cutting safety from the process.
I use those safety glasses, ear plugs, and
gloves when needed. With proper education
and training it becomes natural and
sometimes without even thinking about it.
Not unlike putting my seatbelt on when I
begin to drive.
Most of us have choices. We can get with the
program and support our company's safety
programs or not. Hopefully the people that
are in control of all safety programs will
make the right choice and not only keep a
good solid safety program, but they will
understand that our co-workers, our
neighbors, and our community survive and
demand it.
If you don't mind, I'd like to shift gears.
You know when you get something on your mind
and you seem to think about it everyday?
Well, during the past several weeks, I've
had a young child on my mind. His name is
Timothy and he just turned eight months old.
I do not recall all of the details, but he
is facing life-threatening health issues.
His family has faith in God and that the
decisions made by the doctors and hospitals
will be the right choice. They have asked
for nothing more than thoughts and prayers
from all who know about this little boy. I
have silently expressed that the will of the
Lord be done and I ask everyone else to
pause just a moment here to give thought and
prayer to this young man and his family.
At this writing, Timothy is awaiting the go
ahead for some extremely serious surgery. He
will experience Halloween, Thanksgiving and
Christmas a little different from most
children his age this year, but he will
experience it. Here is a person who has
made no choice to be in this position yet he
remains strong and comforted. We all hope
that safety will be of great importance
during very technical and dangerous
procedures. With strong dedication towards
safety and doing the right thing from the
hands that hold his life, this eight month
old has a positive fighting chance to show
survival.
We wouldn't think of cut backs in safety in
an operating room, so why should we believe
it's okay anywhere else. So when someone
suggests that safety needs to be cut back I
hope that you take a stand and voice your
facts and feelings. A television show called
Hill Street Blues used to end it's opening
with the sergeant saying, "Let's be careful
out there!" We can't afford not to. Timothy
can't afford cutbacks in safety either. Our
prayers are with you Timothy.
Editor's
note: Michael Nance is the NCIC Blue Ridge,
Southern & Western Piedmont areas Safety
Representative. If you are interested in
having one of our programs in your area,
please give Michael a call at 919-218-9047
or email him at Michael.Nance@ic.nc.gov.
|
Abandoned Chemicals
By Mike
Bingham
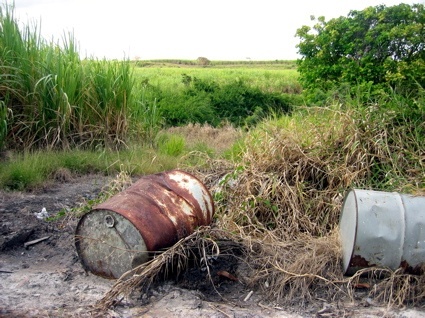
I'll bet you have them. Four
half full bottles of chemical "A". Two cans
of paint "B". A partial bag of substance
"C". No one knows where they came from or to
whom they belong. You got rid of a chemical
last month and now there's a new container
of it in the store room. Walk into another
department and the scene is repeated.
These abandoned chemicals can create
problems ranging from housekeeping issues to
HazCom program violations. Chemicals are
moved, shuffled and worked around until
someone gets tired of dealing with them and
throws them away, maybe sending them into
the environment as a hazardous waste.
A good way to deal with this problem is by
having a good chemical management plan to
supplement your hazard communication plan.
Establish in the plan the procedures used
for getting chemicals brought into your
facility. Who determines the need for a new
chemical? Who assesses the safety issues
encountered when a new chemical is
introduced into the workplace? Who
authorizes new chemicals? How is inventory
managed? When chemicals are no longer
needed, how do we get rid of them safely?
Once these questions are answered and put in
writing, training can begin. More on
training a bit later.
With abandoned chemicals, as with many other
issues, we should think simple. Avoid the
purchase in the first place if at all
possible. A chemical won't be abandoned if
it never made it through your door
initially. It will also never present a
hazard to your workers if it isn't there.
Your up-to the-minute, recently revised
chemical inventory list can be used to see
if there is anything in your facility
already that will do the job you want done.
If nothing suitable is in stock, and a new
chemical is really needed and is approved,
then buy and stock only the very minimum
quantity you need to dependably operate your
business.
Include an "adoption procedure" so people
who need a chemical can access what they
need as easily as possible. Establish
procedures to put partial containers of
chemicals in a secure storage location and
post an inventory list so employees can see
at a glance if a chemical they need is
there. Have a simple requisition method.
This way, employees can use up all of the
material in a container that has been opened
before cracking into a new one. Devise ways
to redistribute these chemicals between
departments or even among different
facilities.
We have to train all employees who use or
are exposed to the chemicals' hazards in the
safe use of those chemicals. Once your
abandoned chemical plan is operational, use
it to show how hazards are reduced or even
eliminated by controlling incoming
chemicals. Show how managing abandoned
chemicals can have a positive impact on
pollution prevention, inventory costs, and
recycling efforts.
Tie it into your housekeeping plan. Keeping
abandoned chemicals stored properly reduces
clutter and reduces the resulting risk of
spills or fires caused by workers trying to
do their tasks around unneeded items. Devise
a way to measure your improvement. Measure
your success by posting the pounds or
gallons of chemicals that were adopted and
used. Success brings success!
And finally, go on the Internet and search
keywords, "orphan chemicals". You can see
what many universities have already done to
address the issue. There is some pretty good
stuff out there.
'til next time!
Editor's Note: Mike
Bingham is the Western Area Safety
Representative for the NCIC, and one of the
10 members of the NCIC's Safety Department
who are out there Working for You!!!to
make N.C. workplaces safer and better by
reducing injuries to employees and saving
money for employers through education and
training. You can contact Mike at:
mike.bingham@ic.nc.us or call:
919.218.9045
|
From the Desk of
Dennis Parnell
Director Safety Education
Cozy Up To Change!
People have many different reasons for
resisting change. Some people (who subscribe
to the old "if it's not broken, don't fix
it" maxim) fail to see how change could
improve their lives. For others, change
represents the unknown and threatens their
sense of control.
While resisting change can do plenty of
damage in your personal life, it can also do
serious damage in your professional life.
Even top employees can gain a reputation for
causing trouble if they're constantly in
opposition to new ideas that might help the
business. Unfortunately, if your
organization is shifting in a particular
direction and you aren't going with it, you
risk, well,
not going with it.
Today's challenging economic environment is
forcing more organizations than ever to
reevaluate the way they do things, and
changes that can increase efficiency or
reduce costs are more valuable than ever.
Employees who cling to the past instead of
looking towards the future might just be the
victims of one of the worst kinds of
organizational changes—a reduction in force.
.
Now you know. Dennis :)
|
CONGRATULATIONS ASHEBORO APCAP
CLASS!
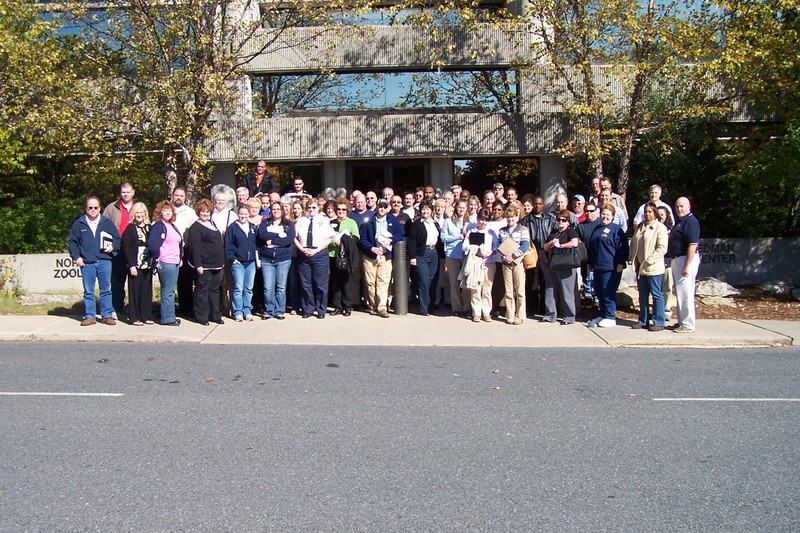
Please join us in
welcoming our last group of 2008 to
complete our Accident Prevention
Certificate Awareness Program.
As always, it is one
of our greatest pleasures
participating in this series of
training throughout our great state.
The networking, learning and
fellowship is
PRICELESS! We look forward to
2009!
|
Insight!
Fun and useless tidbits
Average calories burned daily by the sled
dogs running in Alaska's annual Iditarod
race: 10,000.
A penguin swims at a speed of approximately
15 miles per hour.
A person uses approximately fifty-seven
sheets of toilet paper each day.
Franklin D. Roosevelt was
the only US president elected four
times.
Gerald Ford was the only US president
not to have been elected to either the
presidency or the vice presidency.
Giraffes are the only animals born with
horns. Both males and females are born
with bony knobs on the forehead.
Grover Cleveland is the only US
president to have been married in the
White House.
Hawaii has the only royal palace in the
United States—Iolani.
Hawaii is the only US state that grows
coffee.
|
Coming
November 6 & 18, 2008 AND December 9, 2008,
Smithfield Town Hall
THERE
ARE NOW THREE COURSE DATES AVAILABLE!
Town
Offering Teen Driver Safety Class
Due to the high number of teenage fatalities
on Johnston County roadways, the Town of
Smithfield will offer a four-hour driving
class for teen's ages 15 to 19 entitled
"Alive at 25."
The class
will be held on Thursday, November 6 & 18,
2008 AND December 9, 2008 from 5 until 9 pm
at the Smithfield Town Hall Council
Chambers. The Town will purchase
books for all employees' teen drivers
wishing to attend. Non-town employees'
children will have to pay $5.50 for an
instructional book.
The instructor for the class will be Mel
Harmon with the
N.C. Industrial Commission Safety Education
Section.
For more information or to
sign up for the program call or email
Smithfield Town Clerk
Debbie Godwin at 919-934-2116
Extension1108. |
What Folks Are
Saying
Dennis:
Just wanted you to know how much I enjoyed
the class. All presenters made the
information informative and interesting. One
can tell that there was a lot of planning
and work that was done by everyone involved.
Please thank everyone for me—it was a great
class.
Thanks for best kept secret in NC.
Charlotte Peedin
Director Risk Management
Golden Corral Corporation
Eric
Johnson:
I really
appreciate your conducting the CPR and
First Aid class for us at Variety
Wholesalers, Inc. in Henderson,N.C. on
10-09-2008. I think that everyone in
attendance got a lot out of the class
and you made it interestingto learn what
to do in an EMERGENCY. We will be
looking forward to getting you to
conduct more classes for our education
on different issues.
If I can
pass on to other Business Concerns in
our area to make them aware of what your
"Safety Section" of the North Carolina
Industrial
Commission does for them as well as for
our business feel free to use me as a
reference.
Thomas
Hardie
D.C. Safety
Specialist
Hi Randy,
I want to
thank you very much for being a speaker at
the Guilford County LEPC/ASSE Safety &
Environmental Conference.
Your session
was rated one of the highest. We greatly
appreciate you sharing the information with
the Triad Industrial & Municipal Community.
You do an
amazing job.
Again, I
sincerely appreciate you and all that you
do.
Regards,
Debbie Meurs,
Director, Safety & Health -City of High
Point
Randy,
Great presentation at the conference this
week. That was really the first time that
the NFPA 70E standard was presented that it
didn't go over my head or overwhelm me.
Courtney PopeEHS Compliance
Michael....YOU'RE A HIT!!! See below...
THANKS!!! (many writers wait months and
months to hit print....ya done good!) Linda
----- Original Message -----
From: Jerry Laws
To: L Johnson Sherrard
Sent: Tuesday, October 14, 2008 9:26 AM
Subject: Michael Bingham His article will
make a good Management column, I think.
Good morning, Linda. I read Michael's
article last night and like it. It's a
smart, practical training suggestion that
will work well as a Management column, it
seems to me. I'll make this January 2009's
column.
Thanks again for your help this week.
Jerry
Occupational Health & Safety Magazine
________________________________________________________
I wanted to thank all of
you folks at N.C. Industrial Commission
Safety Education Section for such a
great course, I truly believe in my 32
years of being in Government business
this was the best course that I have
ever sat in on. It is remarkable how all
the instructors work with each other and
I heard a lot of the participants say
they enjoyed the way they presented the
course. Again thank you all and I look
forward to using your services in the
future. PS Please make sure they all
Know this and again THANKS.
Steven O. Paye
Safety Coordinator
City of Asheboro
Asheboro,NC
|
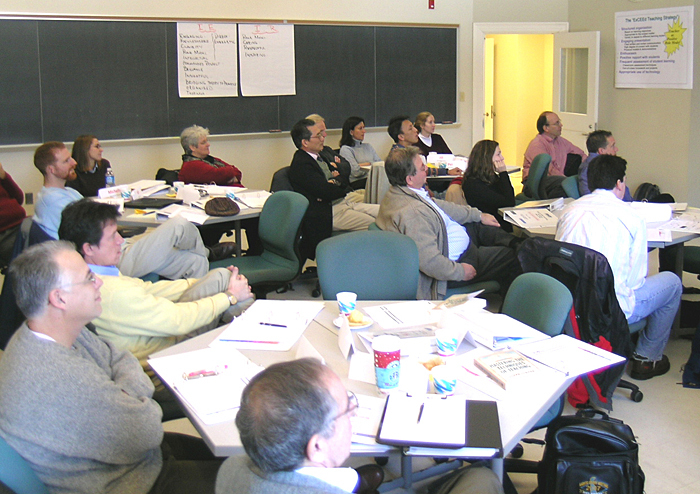
Advanced Accident Prevention Certificate
Awareness Program Coming in 2009
The North Carolina Industrial Commission's
(NCIC) Safety Education Section is wrapping
up the development phase of its new Advanced
Accident Prevention Certificate Awareness
Program (APCAP). This new class is a two-day
event offered only to persons who have
completed any one of the original 30-Hour
APCAP classes that have been offered
throughout the state over the past two
years. It will build on some of the topics
covered in the original 30-Hour and will add
some new subjects.
Subject matter is intended to assist people
with workplace safety responsibilities in
reducing work related injuries and illnesses
by building on concepts presented in the
original 30- hour APCAP.
The first session in the course will be,
"Project
Management for Safety Folks". This
class will cover basic project management
techniques and will provide a foundation for
the rest of the sessions in addition to
providing a durable tool that can be used
over and over again not only in safety, but
in many other business activities as well.
The next session will be a class titled,
"Worker's
Comp How To". It will be presented by
seasoned Worker's Comp personnel from the
NCIC and will provide an excellent
opportunity to get information straight from
the source.
"Body
Mapping for Ergonomics" will build on
the Ergonomics class taught in the original
30-Hour sessions. It will provide a fun,
unique method of identifying and fixing
ergonomic issues.
"Safety and
Health Audits" will be the next class
and will expand upon the 30-Hour APCAP class
"Safety and Health Programs". The activities
will include discussing written plans and
comparing them to the real world of the shop
floor. Gap analysis will be covered.
On the heels of "Safety and Health Audits',
the next topic will be
"Observation-based Safety and Health Audits".
Participants will use a Job Hazard Analysis
(JHA) from their workplace to identify which
behaviors are critical to ensuring safety.
Discussion on how to conduct observations
will be a big part of this session. Previous
30-Hour APCAP classes taught JHA, and the
Observation-based S&H class will put that
knowledge to use.
The first day will conclude with
"Recognition
Programs". In this class participants
will use a template supplied by the NCIC to
fill out a sample written plan that can be
taken back to their workplaces and submitted
for approval.
The second day will begin with
"Safety
Committees", a class on roles and
responsibilities of a safety committee.
Training and motivating the safety committee
will be included as well.
The participants will move into the
"Safety
Math" class which is a basic overview
of common metrics used by employers and
safety personnel. Things learned here will
carry over into the next class, "Selling
Safety to Management".
Up next is
"Safety Rules". In this session
participants will submit their sites' safety
rules to the instructors who will review
them and help fill out an application for
acceptance into a potential money-saving
program related to the NC General Statutes
97-12 rule. If applicable, site visits can
be scheduled for companies who want to take
advantage of this program.
The last class of the event will be
"Contractor
Safety", wherein participants will
fill in a contractor safety sample plan with
their own site's information and have a
second document ready to submit to their
management for approval. Certificates will
be awarded at the end of the second day,
concluding the class.
We will be posting
registration information in December!
|
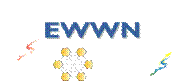
E astern
Water/Wastewater Workshop
December
17, 2008
Please join us for the Eastern Water &
Wastewater Six (6) hour Workshop to be held
in Tyrrell County.
Date: Wednesday, December 17, 2008
INSTRUCTORS: N.C. Industrial Commission
-
ERIC JOHNSON
-
DENNIS PARNELL
Topics are as follows:
- Working in Cold
Conditions
Location:
Tyrrell Hall(Across from Food Lion)
906 Hwy 64
East
Columbia,N.C.
Registration
at 7:45 AM
Classes
begin at 8:00 AM-4:00 PM
Refreshments
at the breaks and lunch will be provided by
the Eastern Water & Wastewater Network.
Cost for the
workshop will be $15.00.
For
additional information and registration,
call or email
PARKER NEWBERN
at
252-331-3044.
|
|
About N.C. Industrial Commission
Safety Section
The N.C. Industrial
Commission Safety Education Section stands
ready to assist you with your Safety
training needs. We offer a variety of
courses, designed to suit your needs. Please
give one of our Industrial Safety
Representatives a call.
DENNIS
PARNELL
Director Safety Education
919-218-3000-Cell
919-807-2602
Dennis.Parnell@ic.nc.gov
 KIM
NADEAU
Program Assistant
919-807-2603
919-218-9049-Cell
Kim.Nadeau@ic.nc.gov
RANDY
CRANFILL
APCAP & APW Coordinator
919-218-2986
Randy.Cranfill@ic.nc.gov
ALVIN
SCOTT
Eastern & Northeastern Areas, Eastern
Defensive Driving Instructor
919-218-2792
Alvin.Scott@ic.nc.gov
WE ARE WORKING FOR YOU!
|
|
|
Quick Links
May 12-15, 2009
EXHIBITORS!
|
Quick Links
One Resort Drive
Asheville, NC
|
Quick Links
North Carolina Safety Congress &
Annual Meeting
November
20-21, 2008
|
Quick Links
NCIC
Mediation
If, after
reviewing the articles, rules, lists, and forms,
you have any questions or wish to obtain
additional information about the mediation
process, e-mail Deputy Commissioner in Charge of
Mediation John C. Schafer.
Click here to e-mail John Schafer, Deputy
Commissioner in Charge of Mediation
READ MORE...
|
Quick Links
National Census of
Fatal Occupational Injuries in 2007
|
Quick Links
Construction
First Day on
the Job
|
Quick Links
General
Industry
Holiday Stress
|
Quick Links
Fleet Safety
Backing Problems
|
Quick Links
SIGN-UP FOR OUR
Email/Newsletter
|
|