Happy New Year Friends in the Name
of Safety:
There is no doubt we all will be
facing many challenges this year,
the economy, jobs and some type of
change.
As you struggle to seek ways to save
resources and money, remember that
the N.C. Industrial Commission is
here working for you every day. Our
staff will make every possible
effort to continue to serve you in
the fashion you have become accustom
to. Please give us a call EARLY in
order to schedule training in 2009.
We have finalized our 2009 APCAP
schedule! We are adding an ADVANCED
APCAP in 2009. In order to
participate, you must have completed
the basic 30-hour APCAP. The
ADVANCED APCAP will be two days of
intense training to further assist
you with your Safety & Health
program.
This year, we will offer BOTH
COURSES concurrently on the same
date and location in order to better
serve you.
Here are the DATES AND LOCATIONS for
2009:
-
February 9-13, 2009 -
Fayetteville, NC
-
March 9-13, 2009 -
Wilmington, NC
-
June 15-19, 2009 -
Smithfield, NC
-
August 17-21, 2009 - Flat
Rock, NC
-
August 31-September 4,
2009 - Atlantic Beach, NC
-
October 26-30, 2009 -
Asheboro Zoo, Asheboro, NC
-
November 2-6, 2009 -
Wilkesboro, NC(Not
confirmed yet)
We look forward to seeing you at
one of our programs in 2009.
Again, let us say "THANK YOU"
for allowing us to be a part of
your family.
Your
REGIONAL SAFETY COUNCILS are
continuing to work for you, so
please refer to the calendar
section of our Safety Bulletin
for more information. Please
support YOUR councils!
As always, we thank you for your
support and we pledge to
continue to serve your needs. We
promise to continue to provide
quality ACCIDENT
PREVENTION training
programs.
|
Dieting in the New
Year:Resolutions that Work!
Millions
of Americans will ring in the
New Year with health and
weight-loss-related resolutions,
but almost a third of
"resolvers" don't even see their
goals through to February. Read
on for four simple strategies to
make this year's resolution
stick:
1. Consider your goal an
evolution, rather than a
resolution, since the latter
implies that if you fall off
course even once, you've failed.
2. Whenever possible, make your
goals flexible: "exercise five
hours per week" is better than
"run five hours per week"
because it can be accomplished
in many different ways.
3. Always focus on what you've
done well towards your
resolution. Rather than dwelling
on the cupcake you ate, or the
exercise you missed, give
yourself credit for packing a
healthy lunch instead of eating
drive-thru, for example.
4. Think of each day as a chance
to make healthier choices, and
give yourself a break - you
haven't failed unless you've
given up, and tomorrow is
another chance to make this
year's resolution stick.
|
Regional Safety Councils
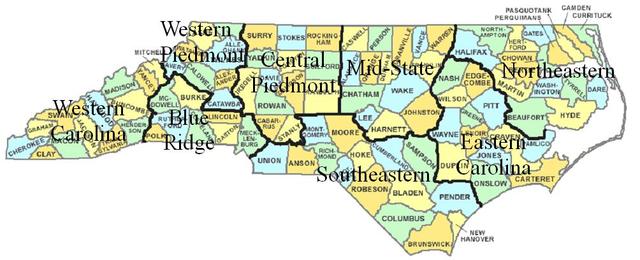
Please do not forget to support
your Regional Safety Councils by
joining their membership ranks
and participating in their
scheduled events. For
membership applications, see the
Quick Links to the right.
|
Fast facts about product
dating:
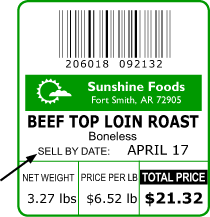
Food product dating tells people
certain information about
specific foods, but there is no
uniform or universally accepted
dating system in the United
States. Except for infant
formula and some baby foods,
product dating is not required
by federal regulations. The
following definitions should
help you understand the dates
that are voluntarily printed on
food products:
Sell by: Tells the store how
long to display the product for
sale. Consumers should not buy
the product after this date.
Best if used by: Tells consumers
how long the product will retain
its best flavor or quality. This
is not a purchase or safety
date.
Use by: Tells consumers the last
date that is recommended for
using the product while at peak
quality. The manufacturer
determines this date.
Closed or coded dating:
Represents packing numbers for
use by the manufacturer to track
inventory, rotate stock, or
locate the product under
suspicion of a problem. These
dates do not indicate freshness
or quality of the product.
|
Check out our
Video Library !
Finally!
We have completed UPDATING our
online Video/DVD listings. The
new listings are in
RED.
To view the rest of our Library
and download the REQUEST FORM,
please
CLICK HERE
|
Parents' Fears NOT Unfounded
For teenagers, it's a huge
milestone, one that they've
looked forward to for years, but
for parents, it's a regular
nightmare. So what's the
occasion? It's birthday number
16 and the potential for a
driver's license. With promises
of freedom and new
responsibility, it's no wonder
15-year-olds are spotted holding
their breath as their 16th
birthday approaches.
But it's also no wonder that
parents are terrified - they
actually have good reason to be.
Not surprisingly, new drivers
have the highest crash risk of
any age group. In 2004, of all
fatal crashes in 2004 that
involved 16-year-old drivers,
driver error and speeding were
involved in 78 and 39 percent of
them (respectively). Nighttime
driving is even more dangerous
for beginners - and the fatal
crash rate is twice as high as
it is during the day.
Luckily, there are things that
parents and teens can do to
ensure that, as new drivers,
teens are as safe as they can
be.
- Don't rely solely on a
driver's education program to
teach a teen to drive. While
this is a good starting point,
it's also smart to make sure
you're comfortable with how your
teen acts behind the wheel.
- Don't expect that your teen is
as comfortable driving at night
as he/she is during the day.
Some students in driver's
education programs never gain
any experience driving in the
dark.
- Restrict the number of
passengers your teen is allowed
to have in the car. Not only can
passengers be a distraction, but
new drivers may feel compelled
to take risks they normally
wouldn't take when driving
alone.
- Require seatbelt use at all
times, remembering that a teen's
habits may change when a parent
or guardian is not in the car.
- Understand and support
graduated licensing programs in
your state. If your state
doesn't have one, you might
consider implementing one of
your own, allowing your teen
increased responsibility over
time.
|
Second Nature
By Michael Nance
As I sat down to think about an
article for the January 09 edition
of our world renowned newsletter, I
found myself thinking about the
situations I've been in and what I
either did right or wrong with
regard to safe work practices. Even
though just a few things resulted in
an incident with minor injury, all
of them were preventable. Well,
with the exception of one and I will
let you be the judge on that.
You have heard the phrase, "When it
rains, it pours" (which was made
famous by the Morton Salt Company).
Beginning the Friday prior to
Thanksgiving is when the flood gates
opened up. Just as my day was
getting started with work, my car
was rear-ended by another motorist
with an estimated 30-35 mph
impact. Everything, and I mean
everything, ended up in the back
seat area. Coffee, notes/papers,
sunglasses and even the garage
remote opener that was firmly
clipped to my sun visor landed in
places I did not know existed in the
car. Fortunately, I did not require
an expensive ambulance ride to the
hospital and neither did the other
party. It did, however, take five
weeks to get my car back.
Preventable? Yes. The other party
simply was not paying attention.
Two weeks later on a Saturday night,
my wife slipped on the bottom step
of the staircase carrying gifts to
wrap. She fell and then let the
rest of the family know about it.
She was in pain and thought she had
broken her right ankle. I
remembered the RICE acronym:
R-Rest, I-Ice, C-Compression, and
E-Elevation. With a little movement
I could tell she did not have a
fracture, but three hours later she
decided to go get x-rays just in
case. Nothing more than a serious
sprain, though a lot of discomfort.
Something that she is still
recovering from as I type.
Preventable? Yes. She didn't have a
clear view of the steps (she'll
break my neck after reading this).
Three hours after we got home from
the Urgent Care, I was working on a
Christmas gift for my wife. I had
purchased a hand blown ornament from
the Blue Ridge Parkway Foundation
store and was making a holder for it
out of wood and copper. I decided
the piece of wood needed to be
trimmed down and drug out my bench
top 6" wood jointer. Properly
plugged in, safety glasses on,
gloves on, push blocks in
use,....still two fingers found
their way into a spinning blade as
the wood ripped out of my gloved
hand along with the push blocks. I
was doing everything I thought to be
correct, following all the required
safety precautions and still got
hurt. I shudder to think that I may
have lost the tip of a finger.
Fortunately, the gloves jammed the
blades as I jerked my hand back. I
only gouged out a chunk. Luckily, it
is almost healed. Preventable?
You be the judge.
Let's see,...another 3 hours passed
and my son got an upset stomach and
really caused a stink,.....well, no
need in getting graphic. About five
more hours passed and my daughter
woke up in the middle of the night
and started talking about how she
"didn't feel" well. I've heard the
whine before and as I was thinking
she was "acting", she hurls on the
bedroom floor. Again, no need to
get graphic here either. Was either
of these preventable? Yes. Too
many sausage balls too fast will
make you sick!
In a 12 hour time span, the Nance
family could have experienced four
Urgent Care visits, even though my
wife was the only one who actually
went. Wow,...that would have been
$200 in co-pays! As I now reflect
on these events, and just a few
others that happened in 2008, I feel
good that I have learned from my
association with other safety
professionals in how to prevent
accidents. Yes, I had some
incidents, but the training I have
received over the years helped me
deal with it and do the right
thing. Five years ago, I would not
have instantly thought of "RICE".
Ten years ago, I would not have
really cared if I had safety glasses
or gloves on when using a
woodworking tool. In 2008, it was
second nature.
Let me ask again,....was the
incident with the finger in the wood
jointer preventable? After all I
was using all required PPE, all
machine guards in place and working,
push blocks in use, etc. A really
good friend of mine introduced me to
three famous safety words a few
weeks after we met (you know who you
are)! Those words were: Speed,
Ease, and Comfort. In honest review
of the "you be the judge" incident,
I left out one key ingredient in the
mix. It is one of the "three
words"....speed. I was probably
feeding the wood too fast into the
cutter blade,....and zap. Safety
jumped up and bit the daylights out
of my finger. I will forever have a
reminder scar.
Let all of us be reminded and honest
with ourselves in 2009 and make
safety "second nature"
Editor's note: Michael Nance is the
NCIC Blue Ridge, Southern & Western
Piedmont areas Safety
Representative. If you are
interested in having one of our
programs in your area, please give
Michael a call at 919-218-9047 or
email him at
Michael.Nance@ic.nc.gov |
Hidden Problem Could Help Silent
Killer
By Mike Bingham
Your
carbon monoxide detector could
assist a silent killer. Some carbon
monoxide detectors have a life span
of only two years. Check yours now
and come back to read the rest of
this article.
I've already delivered my point
above, but read on for a review of
carbon monoxide and maybe some
lesser known facts about it.
It seems strange sometimes how one
thing leads to another once a
subject comes up. I recently had
cause to bone up on carbon monoxide
(CO) for a class that had been
requested. The more I read about it
the more interesting it became. The
old cliché of carbon monoxide being
the silent killer has roots in
reality; CO is a poisonous,
tasteless, odorless, invisible gas.
Signs and symptoms include headache,
nausea, fatigue, dizziness,
drowsiness, chest pain, confusion,
muscle weakness, loss of
consciousness, and death. Carbon
monoxide can have a cumulative
effect. Small daily doses can
accumulate into potentially deadly
doses over time.
One carbon dioxide MSDS I downloaded
gave an HMIS Health rating of 1. As
we know, 1 represents a slight
hazard, and 4 is the most severe
hazard. Why is this deadly gas
given a 1? In this case it is
assumed that the product is used as
intended with all safety measures,
safeguards, and training in place.
If the safeguards aren't in placed
or aren't used, all bets are off.
One of the common uses of carbon
monoxide is as a fuel. The safety
geek in me got all upset and wanted
to know why, if it is used as a
fuel, it kills people who are
exposed to it due to fire or engine
exhaust. We already know that CO is
produced during incomplete
combustion. A little research
showed that CO has an ignition
temperature of 609 degrees C / 1128
degrees F. So, if the original fuel
burns at a lower temperature than
CO, the CO survives as a deadly
byproduct of the fire.
According to the numerous sources,
carbon monoxide poisoning is the
most common cause of accidental
poisoning deaths in the United
States every year. Most of these
deaths are preventable with proper
education and training, and a few
other basic measures.
First, determine whether you need a
CO detector. If you have dependable
electric heat in your home, and will
never use a combustion-based backup
heater or appliance, you won't
really need a CO detector. If you
have all electric forklifts in your
workplace, likewise, you won't need
a CO detector to protect employees
from them. Gas heat or appliances
in the home or workplace or working
around fossil fuel powered forklifts
could trigger different needs and
necessitate installing detectors.
If you get a CO detector, READ THE
OWNER'S MANUAL WORD BY WORD. It
will tell you the specific type of
battery required in some cases. It
will tell you how high to mount the
detector from the floor. CO is
slightly lighter than air, and since
it accompanies combustion, and hot
air rises, the detector needs to be
mounted at prescribed heights - see
the owner's manual for this.
Preventing poisoning by carbon
monoxide includes having preventive
maintenance tasks in place to keep
all equipment capable of producing
it in top working order. If you
lack the tools and expertise to
service the equipment, hire a
professional to do it. Be sure to
test the CO detector and replace the
battery as recommended by its
manufacturer.
Carbon monoxide detectors are simply
tools. They are designed for a
specific job - detecting CO. They
should not take the place of smoke
detectors and vice versa. There are
combination units available, but be
sure you are aware of the CO
detector's life span. As with any
good tool, it needs to be used for
the right purpose. It needs to be
maintained, and its functionality
verified. And it has to be
understood.
Editor's Note:
Mike Bingham is the Western Area
Safety Representative for the NCIC,
and one of the 10 members of the
NCIC's Safety Department who are out
there
Working for You!!!to make
N.C. workplaces safer and better by
reducing injuries to employees and
saving money for employers through
education and training. You can
contact Mike at:
mike.bingham@ic.nc.us or call:
919.218.9045
|
From the Desk of
Dennis Parnell
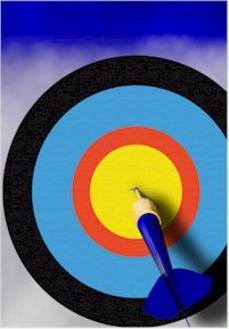
Director Safety Education
January is a good time...
...Take a look at your personal
priorities. With the new year ahead
of you, and the holidays behind, it
might be a good time to look at your
priorities, at work and at home.
Your employer values your hard
work. You do your best to exceed
his or her expectations. You may
have even been rewarded for your
efforts with a promotion or an
increase in your compensation.
Working longer hours than necessary,
even working weekends has become
your "normal" work practice. But is
it too much? Are you out of
balance?
Work is very important, but you need
to take a look at whether or not you
are working too much for your own
good, which is ultimately a
problem. As you place more and more
demands on yourself, you are less
and less likely to realize that this
stress is affecting you. Everyone
has a breaking point; do you know
where yours is?
There might be a need for you to
re-evaluate and make some changes in
your work and personal life
priorities. Ask yourself whether or
not these situations apply to you:
- Taking time off from work seems
difficult, if not impossible.
- You find it hard to relax at home.
- You miss family activities because
you think you need to work.
- Your expectations of yourself are
greater than anybody else's.
- You feel pressured about getting
everything done that "needs" to be
done.
- You have a nagging sense that
failing would be the worst thing
that could happen to you.
If you see yourself in any of these
situations, it is time to take a
long, hard look at your priorities.
Self-induced stress is often
difficult to recognize. A healthy
balance between your working life
and your personal life will lead to
a more satisfying life in the long
run. Get help today if you need it.
Now you know. Dennis :) |
Insight!
Fun and useless tidbits
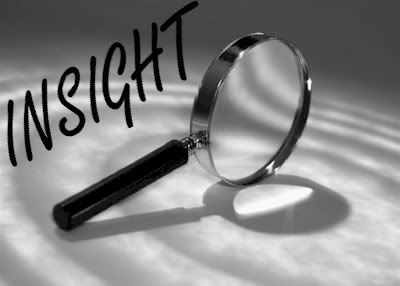
There is only one Q in a Scrabble
game.
The only wood used by famed London
cabinetmaker Thomas Chippendale was
mahogany.
The pecan tree is the only naturally
growing nut tree in North American.
It is native to the Texas,
Mississippi and Mexico River
Valleys.
The only rock that floats in water
is pumice.
The Virginia opossum is the only
marsupial (pouched mammal)
indigenous to North America.
Average length of a coat hanger when
straightened: 44 inches.
Average number of eggs laid by the
female American Oyster per year: 500
million. Usually only one oyster out
of the bunch reaches maturity.
Average calories burned daily by the
sled dogs running in Alaska's annual
Iditarod race: 10,000.
An ear of corn averages 800 kernels
in 16 rows.
|
Savers Credit: A Special Tax Break
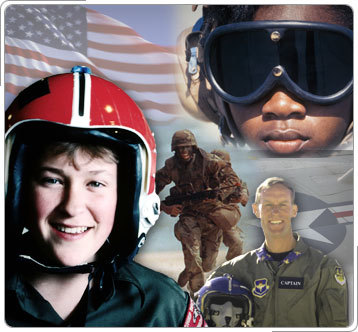
The IRS wants low- and
moderate-income workers to know
about a special tax break called the
Saver's Credit. Workers who
contribute to an IRA, a 401(k) plan,
403(b) plan, governmental 457 plan,
and other retirement programs may be
eligible for this tax break. It is
definitely something you should
investigate!
The Saver's Credit can be claimed
by:
-
Married couples filing
jointly with incomes up to
$53,000 in 2008; $55,500 in
2009;
-
Heads of Household with
incomes up to $39,750 in
2008; $41,625 in 2009; and
-
Married individuals filing
separately and singles with
incomes up to $26,500 in
2008; $27,750 in 2009.
This credit can increase a
taxpayer's refund or reduce the tax
owed. The maximum saver's credit is
$1,000, or $2,000 for married
couples. However, the credit is a
percentage of the qualifying
contribution amount, with the
highest rate for taxpayers having
the least income.
Other restrictions apply:
-
Employee must be 18 years or
older;
-
Employee cannot be claimed
as a dependent on someone
else's return;
-
Employees who are students
are not eligible; and
-
Certain retirement plan
distributions reduce the
contribution amount used to
figure the credit.
If your employer offers a 401(k) or
you have an IRA, you may benefit
from the Saver's Credit. Employees
have until April 15, 2009, to set up
a new individual retirement (IRA) or
add money to an existing IRA to get
credit for 2008. However, only
elective deferrals made to workplace
retirement plans prior to December
31, 2008, are eligible for the 2008
credit.
|
NFPA
releases 2009 Edition of NFPA
70E®
By W. Jon Wallace, CSP, MBA:
Workplace Group
The National Fire Protection
Association (NFPA) issued the
revised 2009 edition of NFPA 70E®:
Standard for Electrical Safety in
the Workplace with an effective date
of September 5, 2008. The 2009
edition of NFPA 70E® contains
numerous revisions. Listed below is
a summary of the major changes:
Contractor Relationships: Article
110.5 requires host employers inform
contractors of known hazards covered
by NFPA 70E® related to the contract
employer's work. The contract
employer shall ensure that each of
his/her employees is instructed in
the hazards provided by the
employer.
Training Requirements - Emergency
Procedures: Article 110.6 requires
employees exposed to shock hazards
that are not reduced to a safe level
by applicable electrical
installation requirements be trained
in approved methods of
resuscitation, including
cardiopulmonary resuscitation (CPR).
The training shall be certified
annually by the employer.
Electrical Safety Program Audit:
Article 110.7 requires the written
electrical safety program be audited
on a frequency established by the
employer.
Arc Flash Hazard Analysis: Article
130.3 requires the arc flash hazard
analysis be updated whenever a major
modification or renovation takes
place. In addition, the analysis
shall be reviewed periodically, not
to exceed five years.
Arc Flash Protection Boundary: The
criteria for the 4 feet arc flash
protection boundary for voltage
levels between 50 and 600 volts has
been modified based on upstream
protection device clearing time of
maximum 2 cycles (0.033 seconds) and
available bolted fault current of 50
kA or any combination not exceeding
100 kA cycles.
Equipment Labeling: Article 130.3
(C) states equipment shall be field
marked with a label containing the
available incident energy or
required level of PPE.
Selection of Personal Protective
Equipment: Article 130.7 contains
several revisions with respect to
arc flash PPE requirements. For
example: Table 130.7 (C)(9) has been
expanded to include additional job
tasks such as performing infrared
thermography as well as other
non-contact inspections outside the
restricted approach boundary.
Additional categories of equipment,
such as arc-resistant switchgear,
have been added to the revised
table. Also, Table 130.7 (C)(10) has
been revised and placed an a more
user-friendly format.
Annex Revisions: The following
annexes have been significantly
revised - Annex F (Hazard/Risk
Evaluation Procedure); Annex H
(Simplified, Two-Category,
Flame-Resistant [FR] Clothing
System.)
Please remember this article is
intended as an overview and not a
comprehensive summary of changes to
the 2009 edition of NFPA 70E®. For
more information on electrical safe
work practices
CLICK HERE for our
January 21, 2009
course at RTP.
If you have any questions concerning
this article or other safety issues,
please contact W. Jon Wallace at
919.933.5548 or e-mail at
jwallace@workplacegroup.net. |
Mulling
it over could cost you your life!
A heart attack is a terrifying
event, and most people assume that
they are dramatic, intense, and
sudden, and while they can be all of
these things, heart attacks are much
more likely to come on slowly,
sometimes causing only mild pain and
discomfort at first.
Unfortunately, misconceptions about
what heart attacks feel like can
prevent people from realizing what
is going on and getting immediate
help. Signs of a heart attack
include:
- Chest discomfort - Could be in the
form of pressure, a squeezing, or
pain that lasts more than a few
minutes. Such pain could stop and
start - don't disregard pain just
because it stops temporarily.
- Pain or discomfort in the upper
body - Can include one or both arms,
the back, neck, jaw, or stomach.
- Shortness of breath - May or may
not be accompanied by other
symptoms.
- Other symptoms - Victims might
also break into a cold sweat or
experience nausea or lightheadedness
during a heart attack.
A heart attack sufferer might not
look anything like the
chest-clutching victim often seen in
the movies, but that doesn't mean
that more subtle symptoms are any
less serious.
Few people are likely to know with
certainty that the symptoms they are
experiencing are associated with a
heart attack, but the fact is that
1.1 million Americans suffer heart
attacks each year.
Being too embarrassed to seek help
or unsure about symptoms are two
good ways to keep from getting the
treatment that could potentially
save your life, or the life of
someone you love. Even if symptoms
seem mild, it's imperative that you
seek medical attention immediately -
treatment is most effective if
administered within one hour of the
onset of symptoms.
|
When to replace your...
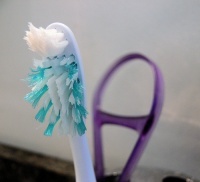
By: Eric Johnson
There's a good chance that you hold
onto certain household items far too
long. It might be because you're
trying to limit waste, because
you're attached to your things, or
because you don't realize some items
should be replaced. While you might
claim to be too busy (or too cheap!)
to replace them, your safety,
health, and hygiene might just
demand that you consider replacing
the following items much more
regularly than you do:
Your toothbrush - The
American Dental Association
recommends that you replace your
toothbrush every three to four
months or sooner if it becomes
visibly worn (the bristles are
frayed or falling out, for example).
It's also a good idea to get a new
toothbrush after you've been ill.
Your pillows - Pillows
trap bacteria, odor, and dust mites
over time. It's a good idea to
preplace your pillows every year.
Your mattress - The
National Sleep Foundation says that
a good mattress can last up to ten
years, so you should at least
replace yours that often. However,
if you typically don't sleep well,
you may find benefits from replacing
your mattress more often (e.g.,
every five to seven years).
Your contact case -
Contact lens wearers are more
susceptible to eye infections than
non-wearers. Properly caring for
your contact lenses and replacing
your lens case every three to six
months can help limit such
infections.
Your tires - Of course,
tire wear depends on many factors,
the most significant of which is how
much you drive. Try inserting a
penny into the tread of your tire.
If you can still see all of
Lincoln's head, the tread isn't very
deep, and it's probably time to
replace your tires.
Your smoke detectors -
You've probably heard that you
should change the batteries in your
smoke detectors at least once each
year, but you should also replace
the smoke detectors themselves every
eight to ten years.
Your fire extinguisher -
Fire extinguishers may lose pressure
over time; it's best to replace them
every ten years.
Eric Johnson is the Mid-State Safety
Representative and Water/Wastewater
Coordinator and covers a fourteen
county area around Raleigh. Please
call 919-218-3567 to schedule
training.
|
|
About N.C. Industrial Commission
Safety Section
The N.C. Industrial Commission
Safety Education Section stands
ready to assist you with your Safety
training needs. We offer a variety
of courses, designed to suit your
needs. Please give one of our
Industrial Safety Representatives a
call.
DENNIS
PARNELL
Director Safety Education
919-218-3000-Cell
Dennis.Parnell@ic.nc.gov
KIM
NADEAU
Program Assistant
919-807-2603
Kim.Nadeau@ic.nc.gov
RANDY
CRANFILL
APCAP & APW Coordinator
919-218-2986
Randy.Cranfill@ic.nc.gov
ALVIN
SCOTT
Eastern & Northeastern Areas,
Eastern Defensive Driving Instructor
919-218-2792
Alvin.Scott@ic.nc.gov
WE ARE WORKING FOR YOU! |
|
|
CENTRAL PIEDMONT SAFETY COUNCIL
|
EASTERN CAROLINA SAFETY COUNCIL
|
SOUTHEASTERN SAFETY COUNCIL
|
WESTERN PIEDMONT SAFETY COUNCIL
Membership Brochure
|
BLUE RIDGE SAFETY COUNCIL
|
NORTHEASTERN SAFETY COUNCIL
|
WESTERN CAROLINA SAFETY COUNCIL
|
NC RURAL WATER ASSOCIATION
|
Peace at Work,
a non-profit dedicated to violence
prevention, in and
through, the workplace believes that
prevention is best way to have a
safe
and secure workplace. Johnny Lee,
the founder and director, is the
author
of Addressing Domestic Violence at
Work and was previously the
Workplace
Violence Specialist for the NC
Office of State Personnel.
Conference
presentations have been provided for
organizations such as the NC
Industrial
Commission, ASSE, NC Safety Council,
Society of Human Resource Managers
and ASIS.
Right now, he is offering a free
trial of an electronic panic button
that
can send summon help with just a tap
of your keyboard, mouse or foot.
More info can be found by
CLICKING
HERE
|
SIGN-UP FOR OUR NCIC SAFETY BULLETIN
Email/Newsletter
|
|